As Australia develops the infrastructure required for electrification, Combilift is ready to deliver powerful improvements to Aussie warehouses.
The forklift manufacturer has been investing heavily in modern technologies to stay ahead of the game, resulting in over 90 per cent of its range being fully electric. Combilift Founder and CEO, Martin McVicar, says it is vitally important for his company to make a positive impact on the environment and its customers’ health. “For Combilift as a company, we’re very focused on how we make our vehicles more environmentally friendly for our customers,” Martin says. “In the last five years, roughly 90 percent of our R&D investment has gone into electric power equipment. So, the majority of the vehicles we’re bringing to market are electric.” As the 21st-century progresses, it’s becoming more apparent that sustainability and electrification are two of the most important pillars of innovation for growing companies. Whether a business works in manufacturing, materials handling, food and beverage, retail, engineering, or a variety of other industries, its customers, investors, and staff will all have one eye on its environmental impact. Knowing this, Combilift has continued to release products with the aim of creating more efficient and less impactful operations. Some of the new electric Combilift models have included the Combi-CB70E and the Combi-CUBE, both of which address their own unique needs. The former is the market’s shortest 7-ton capacity counterbalance forklift, with the ability to handle heavier loads while taking up less space. The latter has also been designed to allow for narrower aisles, but comes with an optional Dynamic 360 steering system, for seamless change of direction.
Combilift also released three more products in 2023 – the company’s 25th anniversary year. These included the autonomous Combi-AGT; the fleet management solution, Combi-Connect; and the Combi-LC blade straddle carrier for the handling of large wind turbine blades and towers. These solutions allow Combilift to fulfil its three pillars of improving safety, maximising storage, and increasing efficiency. Combilift Country Manager for Australia, Chris Littlewood, says the company’s research and that of industry experts point to Australia’s desire for accelerated electrification. “The country has been building in readiness for this next wave of technological innovation. The infrastructure is being put in place and most businesses are trying hard to reduce their emissions,” Chris says. A 2023 report from commercial real estate company, JLL, revealed that 53% of Australia’s top 100 industrial and logistics companies have net-zero targets. With Combilift’s help, it’s hoped that every one of these businesses can achieve their targets, according to Martin. “[Electrification] has been our focus for the last five years, as well as how to measure the efficiency of those trucks,” Martin says. “As a company, we’re inherently focussed on sustainable solutions. And by that, I mean we’re focussed on making vehicles that are more environmentally friendly to use, as well as vehicles that enable our customers to make their warehouse utilisation more environmentally friendly.”
The Great battery debate
To power Combilift’s electrification, Martin has remained a strong voice in favour of lead-acid batteries, despite the automotive industry opting for lithium. This is due to a range of factors, he explains. “In the car industry, the lithium battery has become the norm for electric vehicles, but no one has really figured out how to recycle them effectively,” Martin says. “In seven to 10 years, recycling these lithium batteries could become a challenge if there’s no solutions found. “On the other hand, lead-acid batteries last for much longer and they’re 80% recyclable. So, while we wait for more environmentally friendly alternatives, we feel lead-acid batteries are best.” In 2021, the CSIRO – Australia’s leading scientific research agency – found that Australia recycled 99 per cent of lead acid batteries, while only 10 per cent of lithium-ion battery waste was recycled.
Further, the CSIRO predicts that lithium-ion battery waste is growing by 20 per cent per year and could exceed 100,000 tonnes by 2036. Never one to let down a customer, Combilift will satisfy those who request a lithium battery. However, there is one more reason the company opts for lead-acid over lithium. “Lithium batteries are lighter, which is why the automotive business tends to use lithium – they want the vehicle to be as light and aerodynamic as possible,” Martin says. “But in the forklift industry, no matter what the model is, our vehicles need counterweight to lift the load. So, lead-acid batteries act as that load, instead of adding more steel.”
Rebuild it and they will come
As Combilift continues to innovate and improve its sustainability, it intends on recycling more than batteries. Martin revealed that the lead-acid batteries won’t be the only components being rebuilt in the near future. “Our old premise is only three or four kilometres away, and we still own the premises. So, our intention over the coming years is to set that up as a rebuild centre,” he says. As a proud Monaghan local, this development is sure to bring further jobs and revenue to the community – a value that Martin has maintained throughout Combilift’s proud 25-year tenure in Ireland. “I grew up in this area, and I’ve always desired to stay here. So, to set up a manufacturing company or a business in your hometown gives you great satisfaction,” he says. To Martin, it seems, there could be no more noble cause than to maintain the sustainability of his local community as well as the environment.
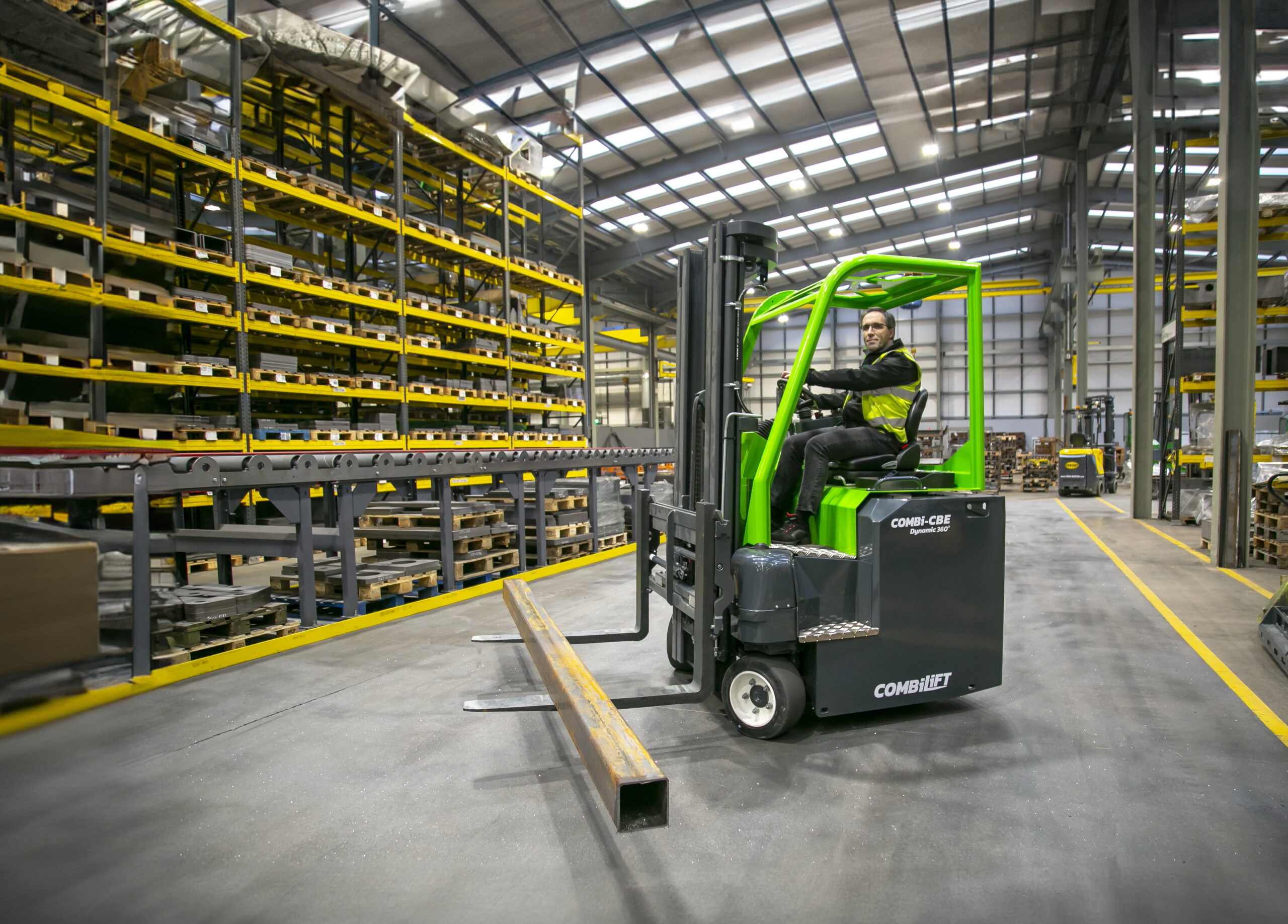