Combilift recently celebrated its 25 year anniversary at the company headquarters in Monaghan, Ireland. In this article, co-founder and CEO Martin McVicar talks about the business’s dedication to improving safety and efficiencies in the Australian market.
Martin McVicar can distinctly remember his first Combilift business trip to Australia. In order to meet a prospect customer, he travelled from Cincinnati in the United States to Brisbane via Chicago, Los Angeles and Auckland.
He can remember shaving in an airport bathroom in Auckland so he would look presentable to demonstrate Combilift’s C4000 truck – the world’s first engine-powered multidirectional forklift – to a steel tubing and pipe specialist later that morning. Combilift received an order from the tube manufacturer as a result.
“I have many stories from over the years, but this one encapsulates an important aspect about the Australian materials handling market, and that is its receptiveness to innovative products,” explains Martin.
“And that’s because Australian businesses are highly focussed on improving efficiency. When it came to that demonstration to the tubing company, they could see straight away how it would help them handle tubing of about six metres a lot more efficiently and safely. To them, it was a no-brainer.”
An inspiring Australian market
Fast forward to today and Australia is Combilift’s fifth largest market – with the US in first position, followed by the UK, Germany and France. One of the reasons Martin says Combilift products are popular in Australia is that each forklift is designed to address a specific market need, and is individually customised to every order.
“For example, the Combilift pedestrian range is the result of an original order from Australia from Bunnings – we custom-built the Combilift Walkie Reach for them,” he adds.
“Today, there are five trucks in that range. In fact, many of our trucks have been inspired to suit Australian customers and every truck we build has been made to order. Our focus has always been on solving customer needs.”
One of the trucks launched to celebrate Combilift’s 25 year anniversary – the Combi-CB70E – also took on feedback from Australian plasterboard company, CSR.
The counter balance, multi-directional forklift is designed to manage long loads but is both compact and electric. It has a patented swivel seat that enables the driver to turn left or right to reduce strain when reversing.
Five products launched in anniversary year
Besides the Combi-CB70E, Combilift launched four other products to celebrate its 25 year anniversary.
“We’re investing an average of seven per cent of our revenue continuously in research and development (R&D), and pride ourselves on innovation, and the launch of these five products underlines that ongoing commitment,” says Martin. “They also are indicative of the specialised solutions that we can provide.”
Among the other machines launched is an autonomous guided vehicle (Combi-AGT), as well as a telematics solution that can integrate with existing fleet management solutions (Combi-Connect) to provide important data on truck maintenance.
The new Combi-LC blade is a remote control operated machine that has been specifically designed for the tandem operation of moving wind turbine blades and towers. Combilift collaborated with Siemens Gamesa to address the load-handling challenges associated with these large blades used in wind energy. The Combi-LC blade has a carrying capacity of 75 tonnes and can move blades up to 150 metres high.
Another truck launched was the Combi-CUBE, an electric counterbalance forklift that has a 360 degrees steering system. This means it doesn’t have to stop and adjust to loads, making it the most manuoeverable truck of its kind on the market.
A greener future with Combilift
As shown in the recent product launches, the majority of Combilift products are now electric. This is just one way the company is committed to a greener future.
“Over 70 per cent of the vehicles we’re currently making are electric and I’d say about 98 per cent of our R&D has gone into electric powered equipment,” explains Martin.
“That’s been our focus for the five years, as well as how to measure the efficiency of those trucks. As a company, we’re inherently focussed on sustainable solutions. And by that I mean, we’re focussed on making vehicles that are more environmentally friendly to use, as well as vehicles that enable our customers to make their warehouse utilisation more environmentally friendly.”
Martin reiterates Combilift’s three pillars, which are: improving safety, maximising storage and increasing efficiency. The company has long had a warehouse design service that they provide to customers free of charge – showing customers exactly how they can unlock every inch of storage space with a warehouse layout.
However, circling back to the electric drive of the company, Martin also mentions that Combilift forklifts use lead-acid batteries instead of lithium. This is because they are far more recylcable, wheras lithium waste is an industry challenge that has yet to be solved.
In fact, according to the CSIRO, only 10 per cent of Australia’s lithium-ion battery waste was recycled in 2021, compared with 99 per cent of lead acid battery waste1.
To summarise, Martin believes that the future is green, in more ways than one with Combilift.
“We’re going to continue to grow our business organically with a key focus on R&D and building products that adhere to our three pillars: improving safety, maxmising storage and increasing efficiency. We look forward to another 25 years of providing the Australian market with sustainable solutions that address their specific materials handling needs.”
Reference: https://www.csiro.au/en/research/technology-space/energy/energy-in-the-circular-economy/battery-recycling
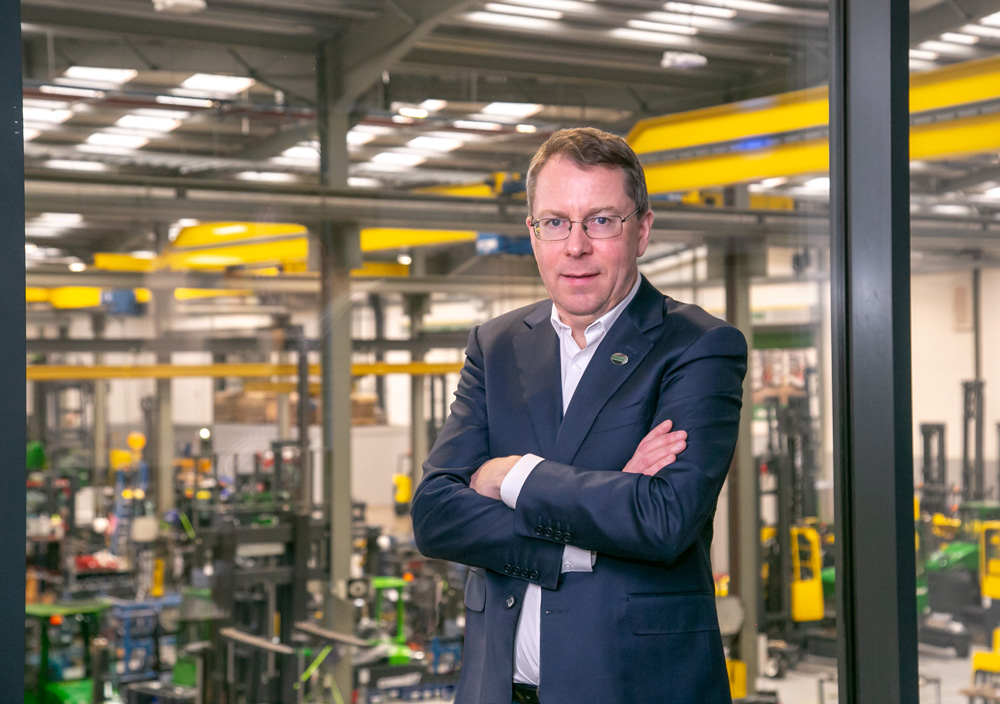