Sustainability is a term that is becoming increasingly important yet has broad meaning. What does it mean for Combilift? CEO Martin McVicar says it’s both part of the company’s value proposition to customers, and an integral part of its own journey.
“Sustainability is at our core – we’re highly focused on making our vehicles more environmentally friendly and helping our customers maximise their warehouse efficiency,” explains CEO Martin McVicar. “But we are also strongly committed to reducing our own carbon footprint, which extends to optimising our resources and minimising waste.”
In terms of delivering more sustainable solutions to customers, McVicar points out that the majority of Combilift’s research and development (R&D) has recently gone into electric forklift trucks.
“I’d say about 98 per cent of our R&D investment has gone into electric vehicle technology, including how to measure the efficiency of those electric vehicles,” he said. “Also, we’re using lead-acid batteries in our forklift trucks which are 98 per cent recyclable.”
The company is also committed to providing its free warehouse layout to customers which has shown to increase warehouse storage by up to 50 per cent. This ability to reduce a physical footprint of a site, translates to reducing the carbon footprint.
“Our free warehouse design brings tremendous value to our customers,” says McVicar. “We do enable them to make their business more sustainable.”
As to Combilift’s own operations – McVicar says the company’s green brand doesn’t just symbolise its Irish roots but reflects its green values. This starts with how the Combilift factory has been designed.
“This encompasses everything from biomass fuel being used in our paint lines, to our lighting and use of renewable energy,” says McVicar. “We remove 473 tonnes of carbon emissions from our production due to biomass fuel. We’re also generating 10 per cent of our daily energy requirements through solar panels.”
Moreover, McVicar points out that 30 per cent of the factory roof space is covered in skylights which enables staff to work in natural daylight. The facility also engages in rainwater harvesting, which is used for jet washing and in employee bathrooms.
Importantly, the componentry in Combilift machines is highly recyclable and McVicar says there are plans to offer rebuilds in the future.
“At the moment, 92 per cent of the components we use in our machines are recyclable,” he says. “Also, our intention is to use our older factory facility – which is also in Monaghan – as a rebuilt centre in a few years from now. This feeds into the circular economy principle which is to keep products and materials in circulation at their highest value.”
Combilift has also switched to water-based paints on all the machines they manufacture, which dramatically reduces the Volatile Organic Compounds (VOCs) used, preventing degradation of the environment.
To summarize, McVicar notes that being accountable to scope 3 emissions will be a challenge for all manufacturers in future. The strategy for Combilift, however, is to source as much as they can locally.
“A large part of our sourcing volume comes from Irish suppliers, many whom we’ve worked with since our beginning – this not only helps sustain the local economy, but it reduces transport emissions, and will enable us to provide traceability and accountability to our scope 3 emissions.”
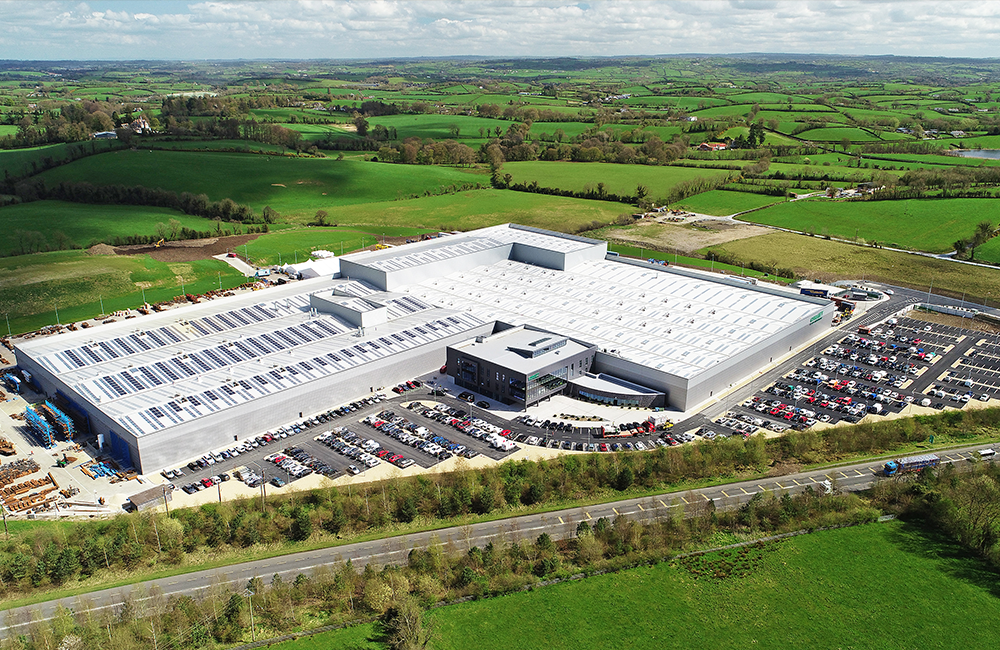